The Rise of 3D Printed Wings: Revolutionizing Industries
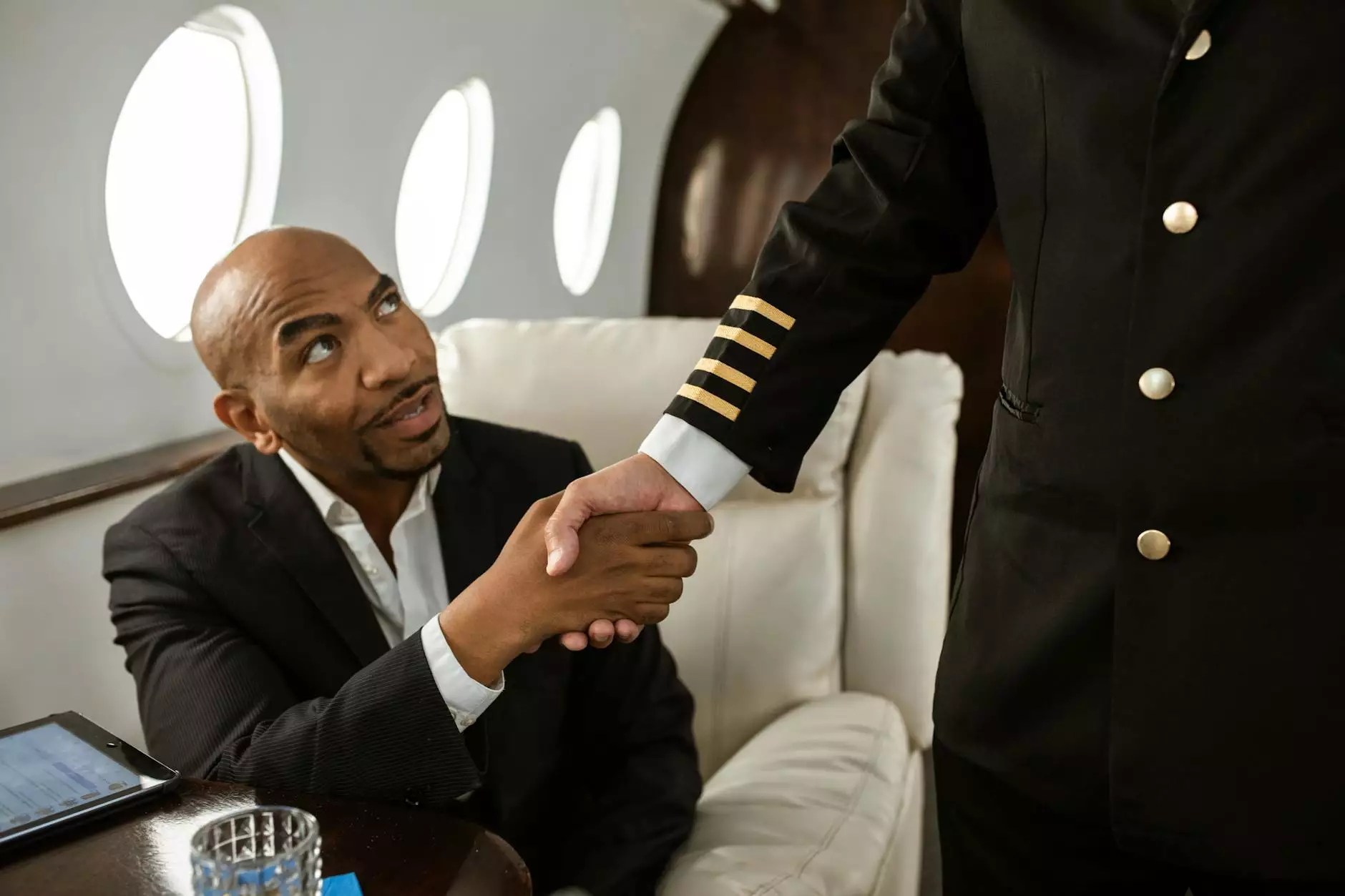
The world of manufacturing has witnessed a digital revolution with the advent of 3D printing. This innovative technology is not just a talking point in tech circles; it is reshaping traditional industries in surprising and profound ways. One of the most exciting applications of 3D printing is the creation of 3D printed wings, which is making waves in the aerospace sector, biomedicine, automotive industry, and beyond.
Understanding 3D Printing Technology
3D printing, also known as additive manufacturing, is the process of creating three-dimensional objects from a digital file. This technology involves laying down successive layers of material until the entire object is built. Here are the key steps involved in the 3D printing process:
- Design: The first stage is creating a 3D model using computer-aided design (CAD) software. This model serves as the blueprint for the final product.
- Slicing: The 3D model is sliced into thin horizontal layers using slicing software. This step translates the design into instructions for the 3D printer.
- Printing: The printer produces the object layer by layer according to the instructions given by the slicing software.
- Post-processing: After printing, the object may require finishing processes like cleaning, sanding, or painting before it's ready for use.
The Advantages of 3D Printing for Wing Design
When it comes to designing 3D printed wings, the technology provides numerous advantages that traditional manufacturing methods simply cannot match. Here are some notable benefits:
- Customization: 3D printing enables highly customized designs that can be tailored to specific performance requirements or aesthetic preferences.
- Material Efficiency: Unlike traditional cutting methods, which waste material in the manufacturing process, 3D printing uses only the necessary amount of material required to create each wing.
- Reduced Weight: The ability to create complex geometries allows engineers to design wings that are both lighter and stronger, contributing to improved fuel efficiency in aircraft.
- Faster Prototyping: The speed of 3D printing allows for rapid prototyping of wing designs, enabling faster iterations and minimizing development time.
- Lower Costs: As 3D printing technologies continue to advance, production costs are expected to decline, particularly for small-scale production runs.
Applications of 3D Printed Wings
The applications of 3D printed wings extend well beyond the aerospace industry. Here are some fascinating examples of their use:
Aerospace and Aviation
In the aerospace industry, 3D printed wings are being used to create lightweight structures that enhance the performance and efficiency of aircraft. Companies such as Boeing and Airbus have started to experiment with additive manufacturing for producing wing components, which not only reduces weight but also minimizes the number of parts that need to be assembled.
Automotive Industry
In the automotive sector, 3D printed wings can be found in race cars where aerodynamics play a crucial role in performance. Custom wing designs can be printed on demand, allowing for rapid modifications and optimizations based on track conditions.
Biomedicine
Interestingly, the principles of 3D printed wings are also finding a place in biomedicine, particularly in the development of advanced prosthetics and implants. The design of wings used in devices can mimic biological structures, offering patients improved mobility and comfort.
Materials Used in 3D Printed Wings
The choice of material is crucial when it comes to printing wings. The most common materials used include:
- Plastics: Such as ABS and PLA, which are lightweight and easy to work with.
- Metals: Such as titanium and aluminum, known for their strength and durability.
- Composites: Combining materials to achieve specific properties tailored to the needs of the design.
Challenges of 3D Printing Wings
Despite the numerous benefits of 3D printed wings, there are still challenges that the industry must address. Some of these challenges include:
- Quality Control: Ensuring consistent quality across different batches of printed wings is vital, especially in safety-critical applications such as aerospace.
- Regulatory Approvals: The regulatory landscape for 3D printed components, especially in aviation, is still evolving, making compliance a complex process.
- Material Limitations: Although materials are advancing, the performance of 3D printed materials may still lag behind traditional materials used in wing manufacturing.
The Future of 3D Printed Wings
The future looks bright for 3D printed wings. As technology continues to advance, we can expect to see:
- Increased Adoption: More industries recognizing the benefits of 3D printing in wing design and production.
- Innovative Materials: The development of stronger, lighter materials that can withstand the rigors of aviation and other demanding applications.
- Sustainability Efforts: Greater emphasis on sustainable practices within 3D printing, including the use of recycled materials and reduced energy consumption.
Conclusion
In summary, 3D printed wings are more than just a technological curiosity; they represent a paradigm shift in how we approach design and manufacturing across various industries. Their numerous advantages, including customization, weight reduction, and material efficiency, suggest a promising future. As we continue to explore and harness the potential of 3D printing technology, we can only imagine the incredible advancements that await us just around the corner. The journey of 3D printed wings is only just beginning, and it is set to revolutionize not only aviation but also countless other fields.
For more insights on the latest trends in 3D printing, visit 3dprintwig.com.