High-Quality Die Casting Parts Supplier: A Comprehensive Guide
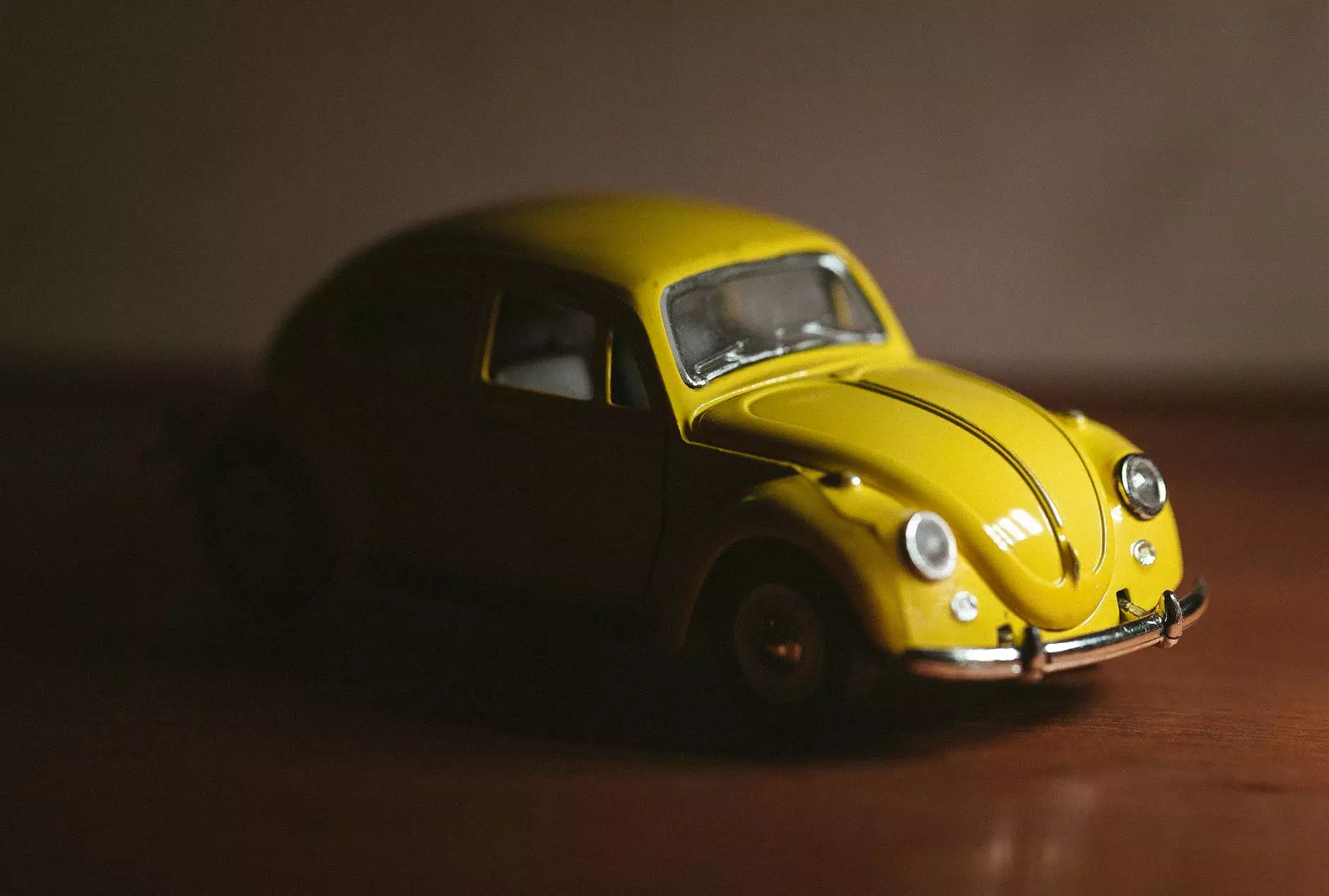
In today's highly competitive manufacturing landscape, finding a reliable die casting parts supplier can significantly impact your production process. Whether you're involved in automotive, aerospace, electronics, or any other industry, the quality of your components is crucial. This article will explore the ins and outs of die casting, the advantages of selecting a top-tier supplier like DeepMould, and what to look for when selecting a die casting partner.
Understanding Die Casting
Die casting is a versatile manufacturing process that allows for the precise formation of complex metal parts. The process involves forcing molten metal into a mold under high pressure, resulting in parts that maintain tight tolerances and intricate designs. Here are essential aspects of the die casting process:
- Materials Used: Common materials in die casting include aluminum, zinc, and magnesium because of their excellent mechanical properties and lightweight characteristics.
- Types of Die Casting: There are primarily two methods: hot chamber and cold chamber die casting. Each method has its advantages depending on the material and application.
- Applications: Die casting is used in various industries, including automotive parts, consumer electronics, and industrial equipment.
Benefits of Choosing DeepMould as Your Die Casting Supplier
When you partner with DeepMould, you're not just choosing a die casting parts supplier—you are selecting a partner dedicated to quality and service. Here are several benefits you can expect:
1. Exceptional Quality Control
Quality is paramount in manufacturing, particularly in industries that demand precision. At DeepMould, we employ rigorous quality control measures throughout the die casting process, ensuring that each part meets industry standards and client specifications. This includes:
- Thorough inspections at every production stage
- Compliance with international quality standards
- Use of advanced quality assurance tools and techniques
2. Advanced Technology and Techniques
Staying ahead of the competition requires that a die casting parts supplier employs state-of-the-art technology. DeepMould invests in advanced equipment and software, which allows for:
- Higher production efficiency
- Reduced lead times
- The capacity to handle high-volume orders without sacrificing quality
3. Customization Capabilities
Every project is unique; thus, customization is essential. Our team works closely with clients to create bespoke solutions tailored to their specifications, ensuring:
- Design flexibility
- Material selection based on performance needs
- Cost-effective solutions for complex projects
4. A Commitment to Sustainability
DeepMould recognizes the importance of sustainability in today's manufacturing environment. As a responsible die casting parts supplier, we prioritize environmentally friendly practices by:
- Minimizing waste during production
- Utilizing recyclable materials
- Implementing energy-efficient manufacturing processes
Factors to Consider When Choosing a Die Casting Supplier
Choosing the right die casting parts supplier is crucial for your business’s success. Here are several factors you should consider:
1. Industry Experience
Assessing the supplier's industry experience can provide insights into their stability and expertise. A reputable supplier like DeepMould has a proven track record across multiple sectors, which underscores our ability to meet diverse client needs.
2. Production Capabilities
The production capacity and capabilities of a supplier are critical. Ensure that your chosen partner can meet your volume requirements and has the equipment to produce parts at the desired quality level.
3. Responsive Customer Service
Timely communication is vital in any business relationship. Opt for a supplier that provides excellent customer support for responsive communication and assistance throughout your project lifecycle.
4. Client Testimonials and Case Studies
Before selecting a supplier, reviewing testimonials and case studies can provide valuable insights into the supplier's reliability and the quality of their work. DeepMould is proud to showcase numerous success stories from satisfied clients.
The Die Casting Process at DeepMould
Understanding the die casting process at DeepMould can help you appreciate the level of detail involved in providing high-quality parts. Here’s an overview of the key steps:
1. Design Consultation
Our team engages with clients during the design phase to optimize the product for die casting, considering factors such as:
- Part complexity
- Material selection
- Manufacturability
2. Engineering and Prototyping
Once the design is finalized, we move to engineering and prototyping. This includes:
- Creation of detailed engineering drawings
- 3D modeling of parts
- Prototype development for testing and validation
3. Tooling Development
In this stage, we focus on the creation of die casting molds. Precision engineering techniques are used to create long-lasting molds that ensure high-quality parts.
4. Production
The production phase involves:
- Heating the metal to its melting point
- Injecting molten metal into the mold
- Allowing the metal to cool and solidify
- Removing the finished parts from the mold
5. Finishing and Quality Assurance
Once the parts are produced, they undergo various finishing processes such as:
- Deburring
- Surface treatment
- Final quality inspections to compliance with specifications
Conclusion
In conclusion, selecting a reputable die casting parts supplier like DeepMould can enhance your product’s quality, optimize production times, and ultimately lead to business success. Our commitment to quality, innovation, and customer satisfaction positions us as a leader in the metal fabrication industry. If you're looking for a partner that values excellence and reliability, look no further than DeepMould.
For inquiries or to discuss your project with our team, visit DeepMould.net, your trusted die casting parts supplier.